Chromium is essential to superalloys
Certain exceptionally demanding applications require the use of superalloys or high performance alloys, these high strength alloys are resistant to corrosion, creep, extreme temperatures and severe mechanical stress. These alloys are usually used in the hottest sections of jets and rocket engines. In a jet engine, chrome nickel is used mainly in the combustion chamber due to the material’s great thermal properties and its ability to withstand harsh working environments and stress at elevated temperatures. These alloys are critical for applications in the aerospace, military, gas, petrochemical, metal processing and nuclear sectors.
For instance, an engine, used for planes such as the Airbus A320 contains about 250kg of chrome metal.
Some chrome-nickel based superalloys can withstand temperature beyond 1400 °C
Properties of chrome superalloys
Chrome-containing superalloys are manufactured using chrome metal, which is almost pure chrome (99.5%). Chrome metal is essential for various types of superalloy as it forms a Cr2O3 oxide film, resulting in good oxidation and corrosion resistance. Some very specific grades of Low Carbon Ferrochrome can also be used to manufacture superalloys. Chrome superalloys provide:
High strength
Resistance to highly oxidising environments
Corrosion resistance
Resistance to extreme temperatures (high and low)
Improved mechanical resistance
Superalloy applications
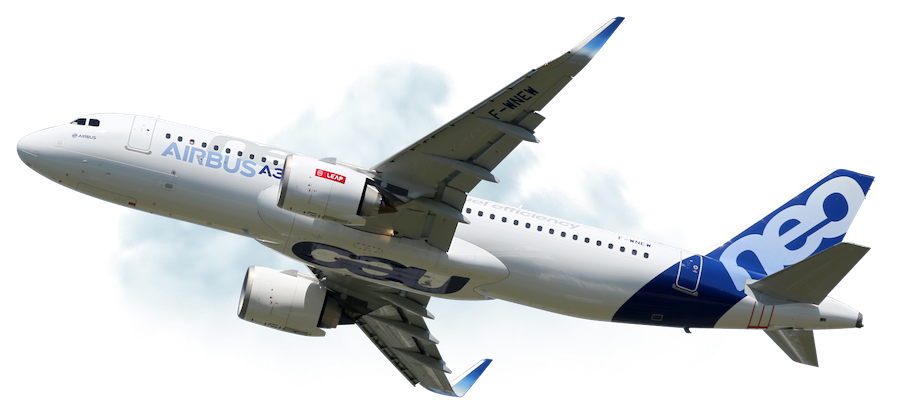
Chrome-nickel superalloys
Chrome-nickel (CrNi) is the most common grade for chromium-containing superalloys, these can be split in four major groups:
- High performance alloys
- Heat resistant alloys
- Corrosion resistant alloys
- Electronic alloys and soft magnetics
Chromium performs several functions in chrome-nickel-base alloys dependent upon the composition and design of the product.
Unique properties ensure the functions of chromium are not easily substituted in chrome-nickel alloys.
Chromium’s functions and properties in Cr-Ni alloys
In alloys designed to offer resistance to wet corrosion chromium improves the material’s resistance to general corrosion as well as localised attack (crevice corrosion). Chromium is essential in the alloys’ resistance to oxidising media such as nitric acid, ferric and cupric chloride. In essence, the higher the alloys’ content of chromium, the better its resistance to attack by oxidising corrodents.
In alloys that offer resistance to high temperature corrosion, chromium is crucial in the alloy’s resistance to oxidation, carburisation and sulfidation. The chromium results in the formation of a protective surface scale at elevated temperatures. As above, increasing chromium content is generally consistent with improved resistance to attack.
Pure nickel is a comparatively ‘soft’ material. However, the addition of chromium (typically 16 to 25%) significantly increases a chrome-nickel alloy’s tensile and yield strength by solid-solution strengthening.
Chromium has a significant effect on the magnetic properties of chrome-nickel-base materials. Pure nickel and nickel-iron alloys are strongly ferromagnetic much like carbon steel. However, the addition of chromium alters this. For example, alloy600, essentially nickel with an addition of 16% chromium, is non-magnetic and exhibits a low magnetic permeability as a result of its chromium content.
Sectors using chrome-nickel alloys
Where chrome-nickel alloys are used
67% of the demand for chrome-nickel alloys is from aerospace, oil and gas, chemical processing and power generation sectors.
Aerospace
The type of aircraft construction determines how much chrome-nickel alloys are used. The main grades consumed in aerospace are alloy 718 and NiFe 36. In jet engines, alloy 718 grades of chrome-nickel alloys are ideal because of their creep, corrosion resistant and heat resistant properties.
They are also used for high-speed airframe parts such as wheels, buckets and spacers, and high-temperature bolts and fasteners.
Aerospace applications account for about 59% of the use of alloy 718 with a chromium content of around 18%.
Alloy 685 with a chromium content of around 18.5% is widely used in some parts of the aircraft gas turbines namely combustion chambers, disks, blades, vanes, casings, and shaft exhaust systems.
Alloy 625 is mainly used in aircraft exhaust systems which must be durable, hard-wearing, tough and resistant to high temperatures. Typical parts are tailpipes, vector nozzles, bellows, and hush kits.
Turbo reactors and gas turbines
Superalloys created from a base of chromium and nickel are the material of choice when it comes to working in high temperatures, such as in elements of a turbo reactor combustion chamber, where temperatures reach 1300 C° and the risk of corrosion is high. Chrome superalloys are also used for land-based gas turbine hot elements where mechanical and creep resistance, as well as anti-corrosion properties are paramount.
Oil and gas
In the oil and gas industry, superalloys are essential in the extreme and highly corrosive environments experienced when drilling in deep water. Given the corrosiveness of the products, the same applies to tanks and turbines used in the chemical and petrochemical industry.
Alloy 625 has good resistance to potable and salt water, and resists attack by chloride ions that can lead to pitting and crevice corrosion. Because of these important properties, it is used widely as clad material or as the main material in pipelines for gathering sour gas. Alloy 625 is also used in seawater heat exchangers in oil refineries and offshore topside applications.
Alloy 825 is used in a wide range of applications such as in the separation of extracted fluids in natural gas production systems or in instances where seawater or certain acids are present. Chrome-nickel alloys (namely Alloy 28, Alloy 825 and G3) are also used in Country Tubular Goods (OCTG) seamless tubes. Alloy 28, which accounts for more than two-thirds of these tubes, contains between 26-28% chromium.
Nuclear
In the nuclear industry, vapour tubes are the only interface between the primary and secondary circuits in a pressurised water reactor. These tubes, made from superalloys, are exposed to extreme conditions, including constant temperature at more than 200 C° as well as high pressure. Alloy 800/800H/800HT is often used for steam-generator tubing in nuclear power plants and other steam superheating tubing or high temperature heat exchangers.
Alloy 750/751 is used in several components in nuclear power plants such as valves or pressure vessels. Alloy 718 is used for nuclear power plant containment vessels and valves. Due to its good resistance to many corrosive aqueous media and high-temperature atmospheres, alloy 690 is used in hardware in nuclear power generation.
Nuclear power is emerging as part of the solution to limit climate change and reduce the reliance on fossil fuels so superalloys will continue to play an important role.
Chemical processing
In the chemical process industry alloy 625 is used where both corrosive media and very high temperatures are present and high-pressure resistance is needed.
Alloy 625 can be welded and fabricated easily and is used in combination with other materials to create thinner-walled vessels for weight reduction without sacrificing heat transfer. It can also be used for bubble caps, tubing, reaction vessels, distillation columns, heat exchangers, transfer piping and valves within chemical processing plants.
Alloy 825‘s chromium content makes it resistant to a variety of oxidizing substances such as nitric acid, nitrates and oxidizing salt.
Automotive
Superalloys are also used in turbo-compressors as well as automotive valves. Corrosion resistance is particularly important here given the high pressure and high temperature conditions, particularly for diesel motors.
Marine
Another major application for chrome-nickel alloys is in scrubbers used in the marine industry to reduce sulphur oxide (SOx) emissions. Scrubbers operate in a highly corrosive environment and require the resilience of chrome-nickel alloys such as Alloy 31, Alloy C276 and Alloy 59.
Alloy 725 is resistant to hydrogen embrittlement and stress-corrosion cracking, and, as such, is used for hangers and high-strength fasteners used in marine applications.
Also, Alloy 625 can be found in marine applications such as wire ropes, propeller blades, propulsion motors and sheathing for undersea communication cables.